ET23SWE0058 - HVAC Capacity Controller
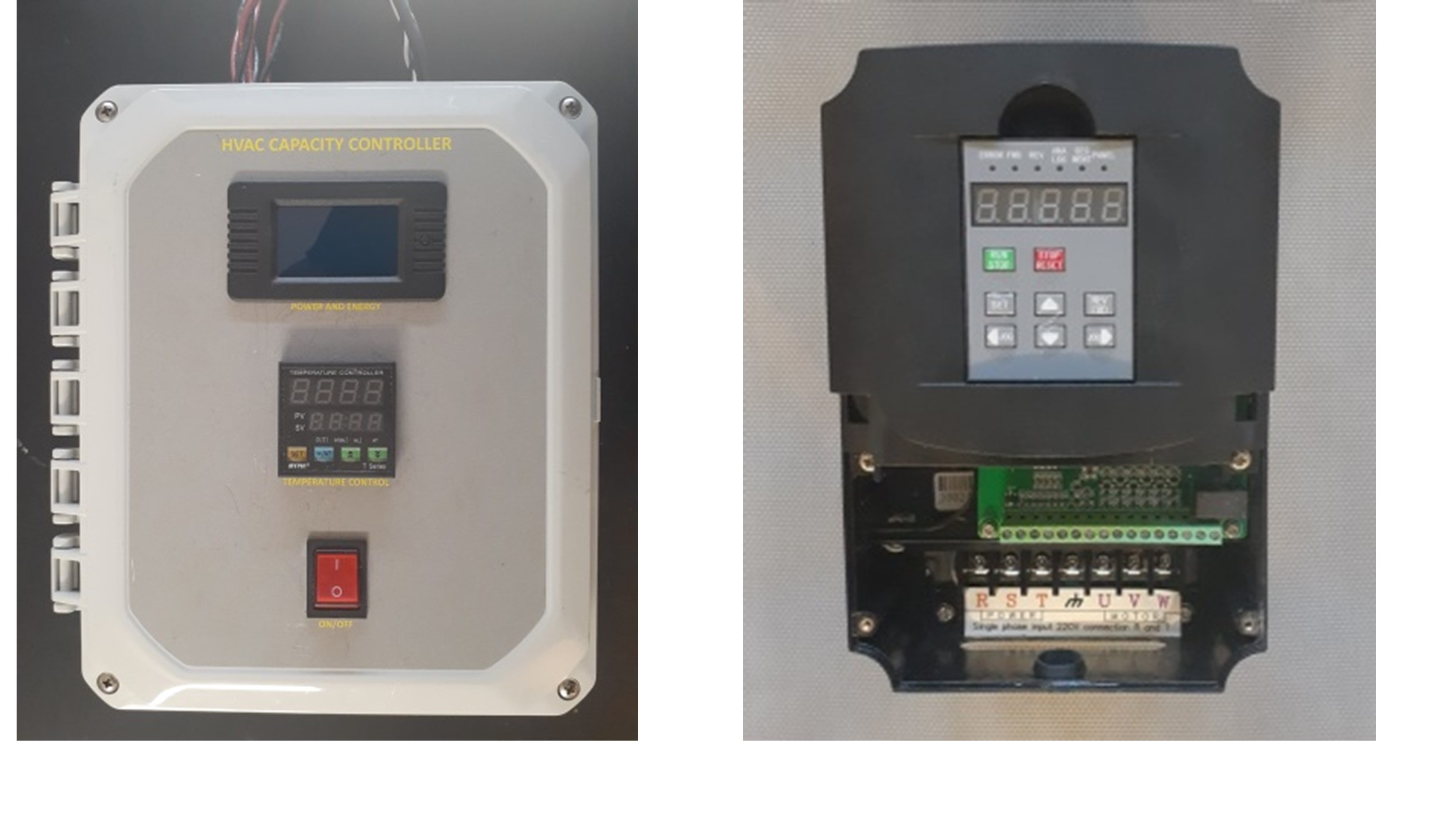
Problem: For residential and commercial consumers seeking to reduce their energy consumption and carbon footprint and to promote a more sustainable future for their local communities and economies, variable frequency drives (VFDs) deliver significant efficiency improvements and a quick return on investment (ROI). Although adding a VFD to existing “fixed-capacity” or “fixed-speed” heating, ventilation, air conditioning and refrigeration (HVACR) equipment can drastically improve overall efficiency, a standalone VFD would have to be manually controlled or adjusted to achieve optimum efficiency improvements. Therefore, to maximize the benefits of retrofitting VFDs to existing “fixed-capacity” or “fixed-speed” HVACR equipment, control systems that provide the proper input information to the VFDs must be included.
Solution: Go Solar America (GSA) has developed and demonstrated an HVAC Capacity Controller (HCC). The HCC is a standalone device capable of interfacing with the multitude of off-the-shelf VFDs currently available on the market. The function of the HCC is to provide the signal inputs to the VFD so that the VFD’s output supplies the correct voltage and frequency that produces improved load matching, less on and off cycling, soft start-ups, and faster temperature pull-downs of the HVACR system. The two main inputs required by the VFD to control the HVACR compressor’s speed are temperature and remote start. A temperature probe or sensor is installed in the “return-air-duct” to sample the temperature in “space to be cooled”. The probe produces a small voltage that is directly proportional to the “return-air-duct” temperature and is fed into a temperature transducer. The temperature transducer converts the small voltage to a 0-to-10 volt signal that the VFD requires to vary the frequency and the speed of the HVACR compressor automatically. The VFD requires a “dry contact” input (switch) to remotely start the VFD. The thermostat in the “space to be cooled” starts the cooling or heating process by sending a signal to the HCC which in turns send out the “dry contact signal to the VFD starting the HVACR compressor. There are many high-efficiency HVAC systems currently available for both residential and commercial applications; however, for the millions of “fixed-capacity” or “fixed-speed” systems already installed, there are not widely available off-the-shelf, easy-to-install retrofits that provide the control inputs required by VFDs to produce the desired efficiency and environmental improvements. Therefore, retrofitting the HCC and a VFD to existing “fixed-capacity” or “fixed-speed” HVACR equipment allows owners and operators the ability to implement a variable-capacity modulation strategy that reduces energy consumption while performing the same amount of work. Adding a VFD to a “fixed-speed” compressor motor can result in a 30 to 50 percent reduction in energy costs while enabling capacity modulation from 40 to 100 percent without having to replace a compressor.
Proposed Project: Go Solar America proposes to conduct a “Field-Study” of their HCC interfaced with various off-the-shelf VFDs to retrofit various types of “fixed-capacity” or “fixed-speed” HVACR equipment. Participants in the study shall include a school and several single-family residences. The participants shall be located within the Southern California Edison-service area, allowing the project team to take advantage of data provided by installed smart utility metering. The data can be used to evaluate reductions in energy consumption and demand. The objectives of the study are to:
- Select the best VFDs to be interfaced with the HCC
- Select the best HVACR equipment to be retrofitted
- Determine net reductions in energy consumption and demand
- Determine estimated operating cost savings of retrofitting existing HVACR equipment
- Determine the Short- Term-Reliability (STR) of the interfaced HCC, VFD and HVACR equipment. The STR describes how often the HCC/VFD upgrades or HVACR equipment malfunction within the first 6 months of service installation dates.
Determine system operating procedures, settings and parameters, such as; minimum and maximum frequencies, temperature, starting torque, ramp up time, etc.